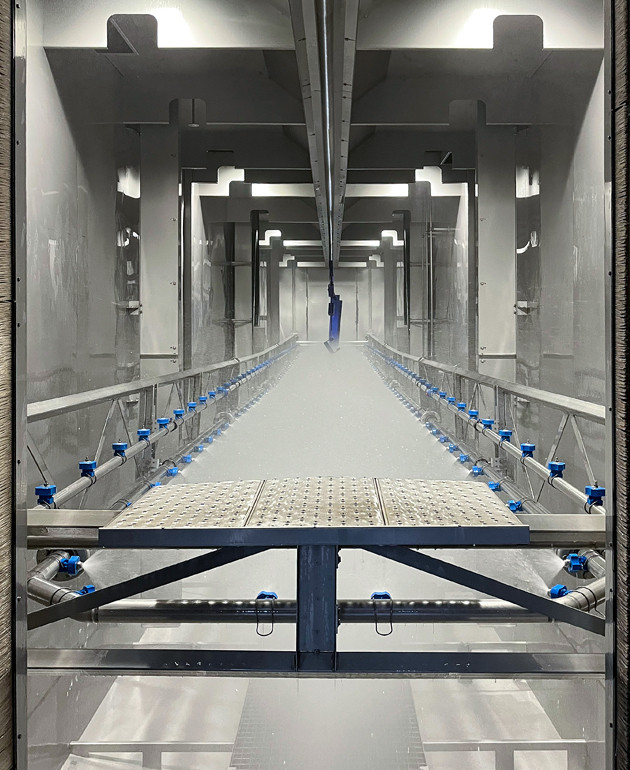
RIPPERT-News Pulverbeschichtungsanlage mit patentierter VBH bei Hoffmeister
Vorbehandeln und Pulverbeschichten von XL-Werkstücken bis 16.700 mm in kleinen Losgrößen.
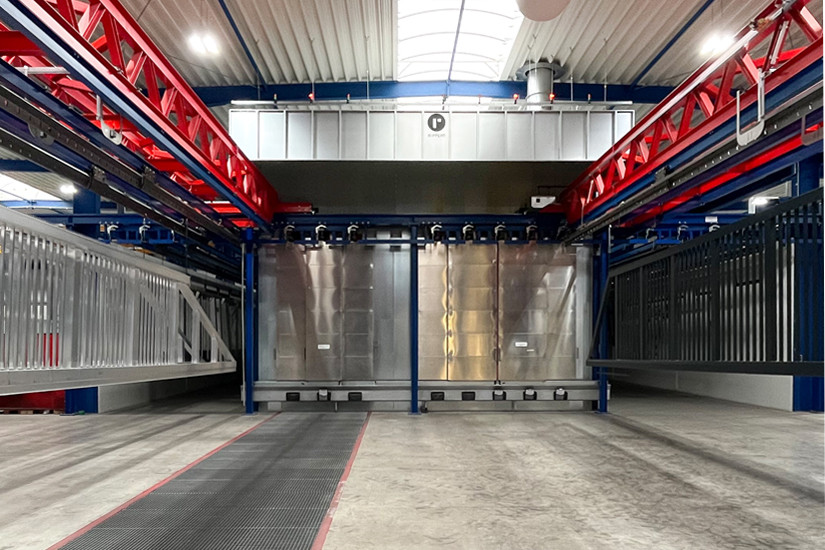
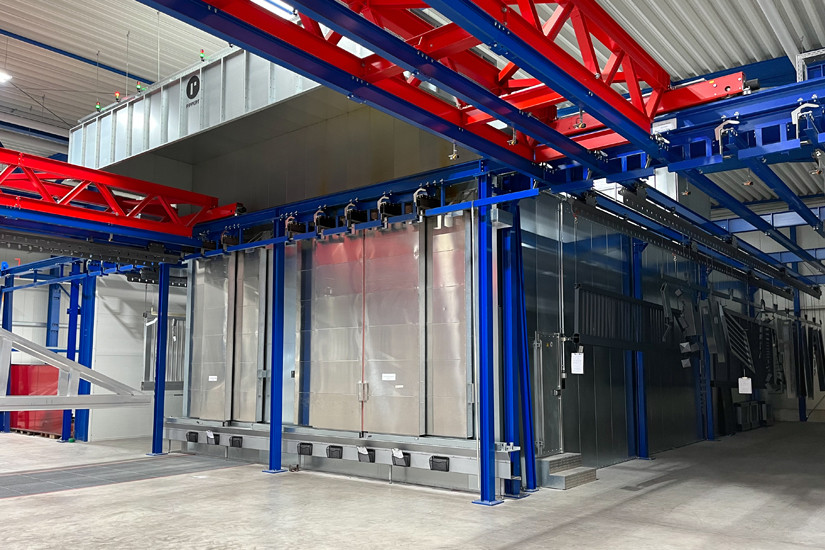
Die Aufgabenstellung der neuen Pulverbeschichtungsanlage bei Fa. Hoffmeister lag darin, einen effizienten Prozess für XL-Werkstücke bis 16.700 mm, in kleinen Losgrößen, mit einer qualitativ hochwertigen Beschichtung zu realisieren. Zum Einsatz gekommen sind eine neuartige 6-Zonen Vorbehandlungsanlage auf kleinstem Raum sowie ein Ofenkonzept mit Abwärmenutzung. Die Firma Hoffmeister aus Brakel ist seit Jahrzehnten auf die Entwicklung, Produktion und Vertrieb von Toranlagen für alle gewerblichen und privaten Einsatzgebiete spezialisiert. Das Portfolio umfasst Garagen- und Industrie-Sektionaltore, Rolltore sowie freitragende Falt-, Schiebe- und Kombinationstore aus Aluminium und Stahl. Die moderne, freitragende Konstruktion ist die Spezialität der Firma Hoffmeister. Sie kann Hofeinfahrten von 40 m Breite und mehr abdecken. Diese Vielfalt an Produkten galt es, bei der Planung der neuen Pulverbeschichtungsanlage zu berücksichtigen. Der Materialmix aus Aluminium, Stahl und stahlverzinkten Bauteilen war eine weitere anspruchsvolle Aufgabe für die „richtige“ Vorbehandlung. Ebenfalls ist die Energieeffizienz der Anlage für so große Bauteile sowie die zur Verfügung stehende Aufbaufläche zu beachten. Funktionsbeschreibung Die Aufgabe der Werkstücke erfolgt an der Hub- und Senkstation ergonomisch durch den Werker. Zusätzlich kann die Anlage direkt mit dem Hallenkran bestückt werden. Die Aufgabestation liegt in einem von der Anlage getrennten Hallenbereich. Die angehangenen Werkstücke werden nun manuell auf die Querverschiebebühne geschoben. Dies ist auch, dank der gelagerten Schwerlastrollen, bei der Maximalbelastung problemlos möglich. Die 2 Querverschiebebrücken sind elektrisch betrieben und werden vom Bediener an die entsprechende Position gefahren. Um einen reibungslosen Prozess (Beladen/Behandeln/Abnehmen) zu gewährleisten, sind insgesamt 15 Pufferplätze im Anlagebereich verteilt die über den Querverschub angefahren werden können und ein „Überholen“ ermöglichen. Durch die Größe der Bauteile und die Variabilität der Prozessfolge ist Wahl auf eine Traversentechnologie gefallen. Vorbehandeln Für die Langlebigkeit der Produkte aus dem Hause Hoffmeister ist die Beschichtung ein wichtiger Aspekt weil die Außentore, der ständigen Witterung und Salzfrachten durch Fahrzeuge im Winter ausgesetzt sind. Eine gleichmäßige Vorbehandlung ist hierfür besonders wichtig. Aus diesem Grund ist keine herkömmliche Horizontalbeaufschlagung eingesetzt worden, sondern eine patentrechtlich geschützte Neuentwicklung von RIPPERT. Die Innovation ist die vertikale Führung der Düsenkränze über das Bauteil mit frei progammierbaren Geschwindigkeiten und Zeiten. Die Reinigung der Bauteile sowie die Spülung erfolgt in der Hauptkammer in verschiedenen einstellbaren Prozessschritten. Das Vorbehandlungsverfahren ist mit Fa. NABU ausgearbeitet worden, um einen hohen Korrosionsschutz zu gewährleisten. Trocknen / Pulvern / Einbrennen Nach dem Prozess Vorbehandeln werden die Bauteile dann wieder auf die Querverschiebebühne geschobenen und anschließend zum Kombitrockner (Pulvereinbrennofen/Haftwassertrockner) gefahren. Der PEO (Pulvereinbrennofen) ist aktuell noch gasbeheizt (Elektrisch/Biogas ist in Planung). Der HWT (Haftwassertrockner) wird über das Abgas vom PEO sowie dessen Abluft beheizt, d.h. der HWT hat KEINE eigene Beheizung. Über eine spezielle Programmierung der Startphase, ist eine schnelle Aufheizung des HWT weiterhin gegeben. Diese Abgas-/Abluftnutzung hat erhebliche Vorteile für die Energieeffizienz der Anlage. Nach dem HWT Prozess werden die Werkstücke dann zum nebenliegenden Abkühlpuffer gefahren und anschließend dann zur automatischen Pulverkabine. Das automatische Pulvern wird über einen manuellen Startimpuls für den Transferbetrieb gestartet. Der Transferförderer zieht die Laufwagen aus einem dafür vorgesehenen Pufferplatz in die Pulverkabine und fährt diese dann einmal komplett durch die Pulverkabine und anschließend zurück. Die nun automatisch/manuell gepulverten Bauteile werden dem PEO für den zeitgesteuerten Einbrennprozess zugeführt und anschließend über einen Kühlpuffer zur separaten Abnahmestation mit Hub- und Senkstation gefördert werden. Nach der Abnahme findet die Endmontage der Tore statt.
Vorbehandlung der XL-Teile mit patentrechtlich geschützte Neuentwicklung von RIPPERT.
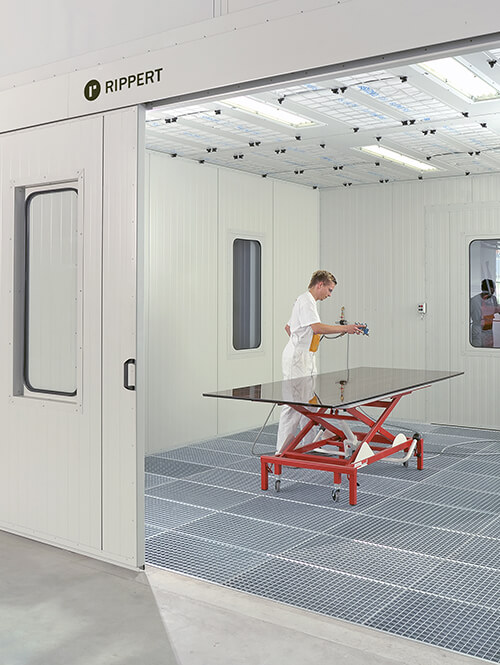