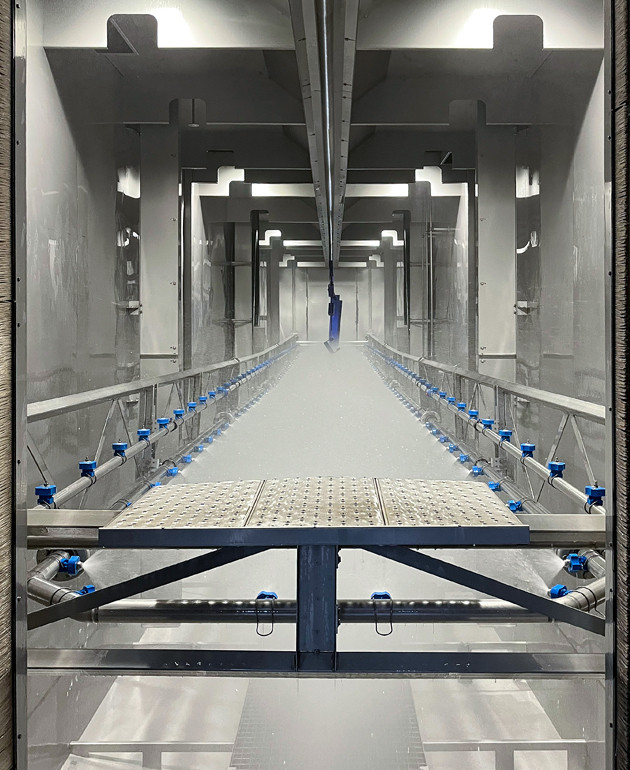
RIPPERT-News Powder-coating plant with patented pre-treatment at Hoffmeister
Pre-treatment and powder-coating of XL workpiece in small batches.
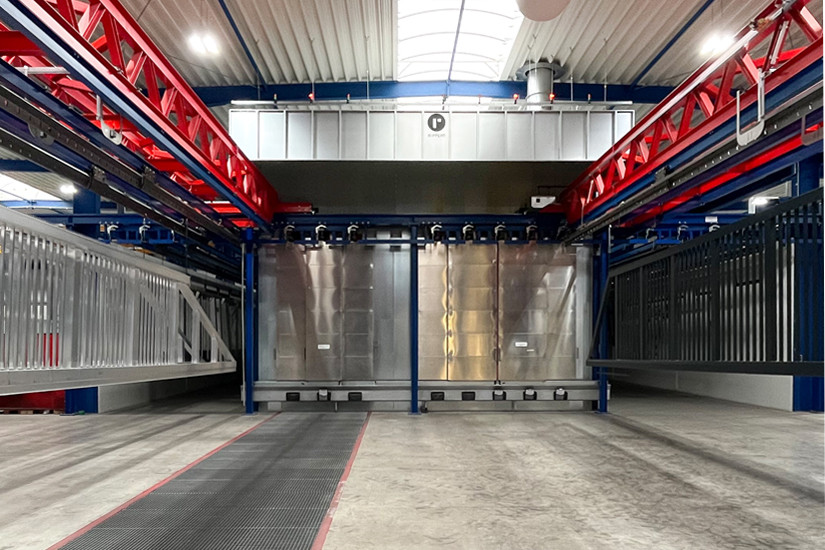
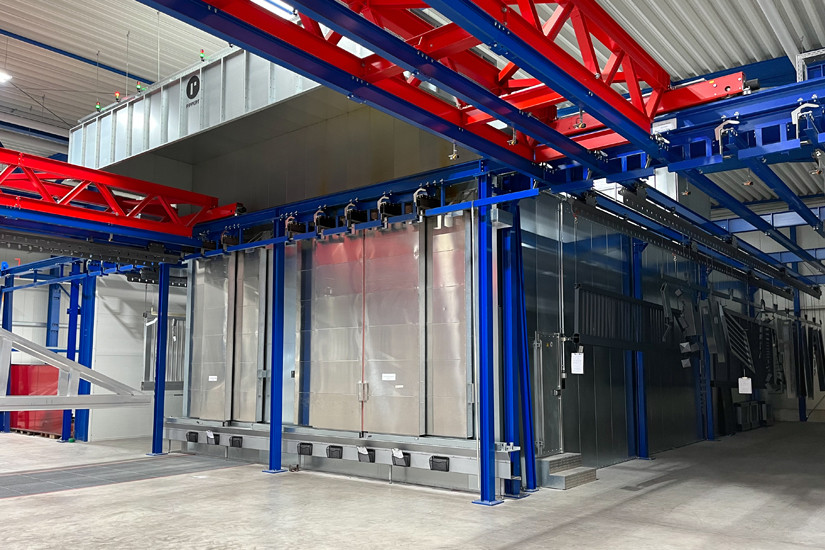
The task of the new powder-coating plant at the Hoffmeister company was to implement an efficient process for XL workpieces up to 16,700 mm, in small batches, with a high-quality coating. An innovative 6-zone pre-treatment plant in the smallest space as well as a furnace concept with waste heat utilisation were installed. The Hoffmeister company from Brakel has specialised for decades in the development, production and sale of doors for all commercial and private areas of use. The portfolio encompasses garage doors and industrial sectional doors, roller doors and self-supporting folding, sliding and combination doors made of aluminium and steel. The modern, self-supporting construction is Hoffmeister’s speciality. It can cover yard entrances with a width of 40 metres and more. This wide variety of products had to be taken into account in the planning of the new powder-coating plant. The material mix of aluminium, steel and galvanised steel components was a further demanding task for the “right” pre-treatment. The energy efficiency of the plant for such large components as well as the available installation area also has to be observed. Functional description The workpieces are fed in ergonomically by the worker at the lifting/lowering station. In addition, the plant can be loaded directly with the hall crane. The feeding station is located in an area of the hall that is separated from the plant. The suspended workpieces are now pushed manually onto the cross-transfer platform. Thanks to the heavy-duty rollers this is no problem even under maximum load. The two cross-transfer bridges are driven electrically and moved to the corresponding position by the operator. To ensure a smooth process (loading/treatment/removal), a total of 15 buffer stations are distributed in the plant area. These can be driven to via the cross transfer and enable “overtaking”. The transverse technology was chosen due to the size of the components and the variability of the process sequence. Pre-treatment Coating is an important aspect for the durability of the products from Hoffmeister, because the outside doors are constantly exposed to weathering and salt carried by vehicles in winter. Homogeneous pre-treatment is particularly important for this. For this reason, a conventional horizontal application is not used, but rather a patent-protected new development from RIPPERT. The innovation is the vertical guidance of the nozzle rings over the component with freely programmable speeds and times. The cleaning and rinsing of the components takes place in the main chamber in various adjustable process steps. The pre-treatment process was developed in collaboration with the NABU company in order to ensure a high degree of protection against corrosion. Drying / powder-coating / curing Following the pre-treatment process, the components are pushed back onto the cross-transfer platform and then transported to the combination dryer (powder curing oven/residual water dryer). The PCO (powder curing oven) is currently still gas-fired (electrical/biogas is planned). The RWD (residual water dryer) is heated by the PCO and its exhaust air; i.e. the RWD has NO heating of its own. Fast heating of the RWD is still possible via special programming of the start phase. This use of exhaust gas/exhaust air has significant advantages for the energy efficiency of the plant. Following the RWD process, the workpieces are transported to the adjacent cooling buffer and subsequently to the automatic powder-coating booth. The automatic powder coating is started by a manual start pulse for the transfer operation. The transfer conveyor pulls the trolleys out of a buffer station provided for the purpose into the powder-coating booth and then drives them once completely through the powder-coating booth and then back. The now automatically/manually powder-coated components are fed into the PCO for the time-controlled curing process and subsequently transported via a cooling buffer to the separate removal station with lifting/lowering station. The final assembly of the doors takes place after removal.
Pre-treatment of the XL parts with patent-protected new development from RIPPERT.
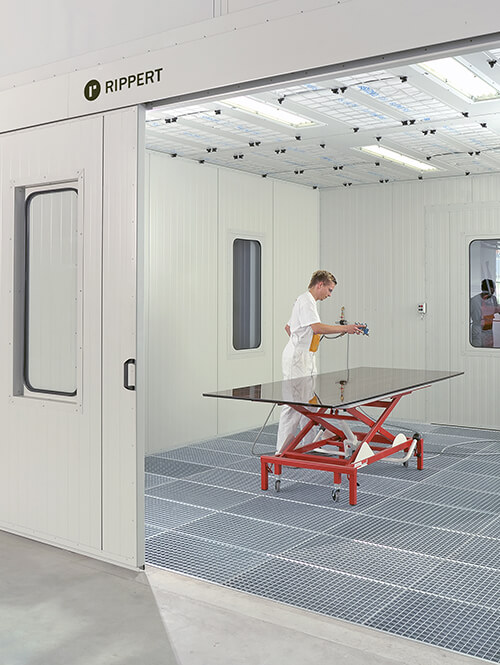