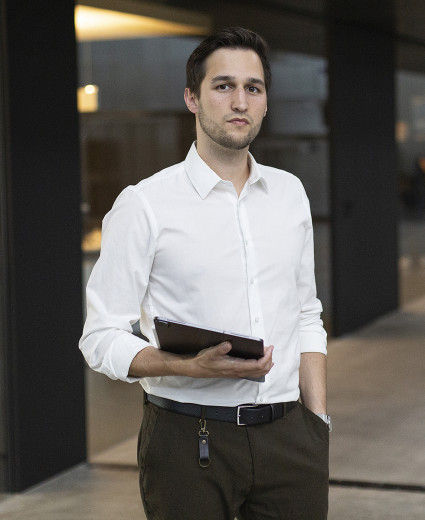
Marco Frasch – Project Manager Conveying Systems It is always exciting because the projects are clearly different from each other.
I first came across the name RIPPERT during my apprenticeship as an industrial mechanic. A coating plant from RIPPERT was in use at the company where I was working at the time. The service and maintenance of the plant was part of my task field – that has stuck with me.
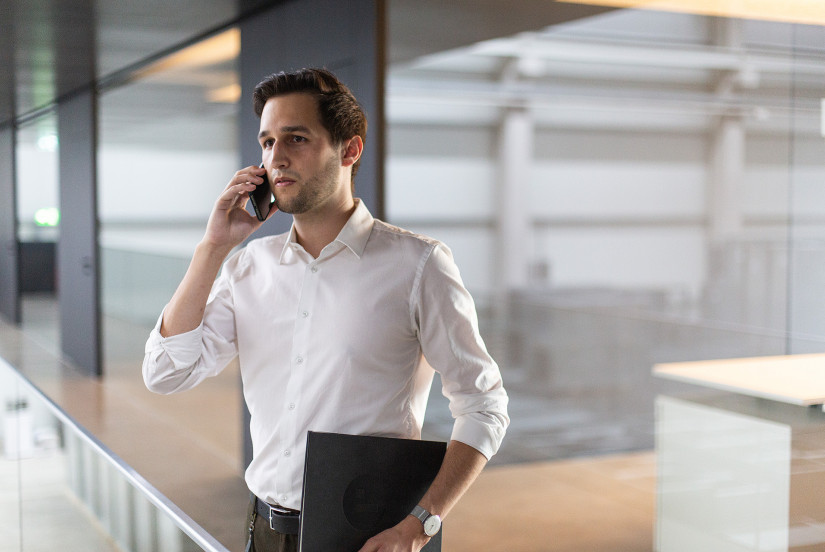
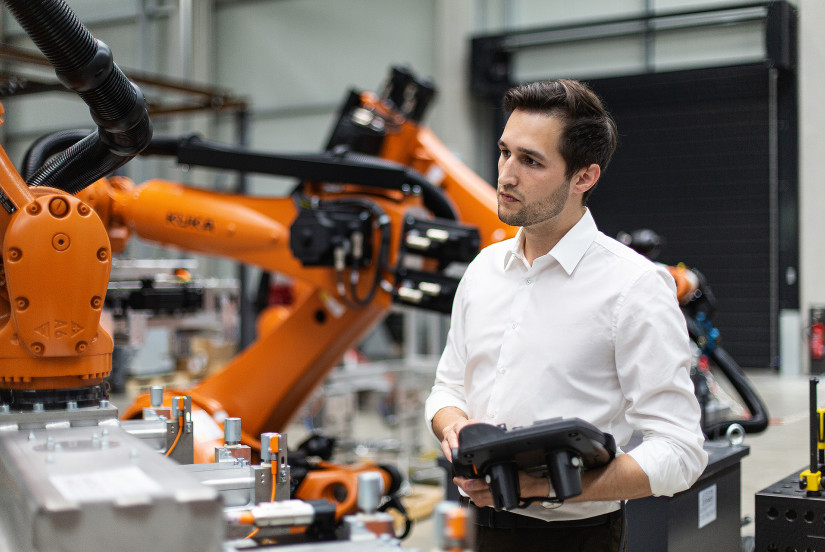
After studying mechanical engineering at the University of Applied Sciences in Soest, I sent a speculative application to RIPPERT in 2013 for a practical semester – and was promptly accepted. I was employed in the Conveying Systems department, where I designed several special conveyors and attended to various projects. In the context of my degree thesis, I concerned myself with automatic lubrication systems for conveyors. After graduating, I spent a few more months in the department before taking a break in 2014 to obtain a master’s degree at a university in Edinburgh. My master’s thesis revolved around the topic of energy efficiency. It concerned an analysis of energy-saving lamps, in particular LED technology. Today, everybody – naturally at RIPPERT, too – is talking about energy efficiency, in particular the saving of CO2. An example? In conveying systems, energy can be saved sustainably, for instance with travel paths or smaller sized cross-beams. We support our customers here with the RIPPERT know-how. Following my year of study in Scotland, I immediately started again at the company headquarters in Herzebrock-Clarholz, where I was able to apply my knowledge, this time in the position of team leader in Conveying Systems. Unlike other departments at RIPPERT, we are less concerned in Conveying Technology with the construction of our own plants and more with the purchase of suitable components. As team leader I am involved in every step of the process, from obtaining quotes from suppliers to the commissioning of the plant. This is always exciting, because the projects sometimes differ significantly from one another. We also carry out on-site checks of the progress of the construction work for the plants planned by us. As a result of that I get around a lot: for example, I’ve been to South Germany, France, the Netherlands, Switzerland, Czechia, Slovenia, Slovakia and Taiwan. Of course, it’s a nice side effect to be able to get to know the world better in this way. What’s important in my profession? Organisational talent and flexibility! After all, the work is very varied. It includes regular discussions with our project participants, and of course with our customer and suppliers, too. There’s no question that the market environment has changed. When I started at RIPPERT in 2013, quite simple plants were still in demand; that has become more complex and extensive. Let’s just take the buzzword Industry 4.0. Computer-assisted conveying systems are more in demand. For us, that means staying on the ball. We have customers from the most diverse branches of industry. It might be to do with the manufacture of bicycles, or another time kitchen products or agricultural machinery. Every enquiry is different. Actually, we don’t have any plants that can easily be copied. What I have noticed with many projects is that RIPPERT has a very good reputation in the market. I can still remember a holiday flight and a conversation I had on the plane with the passenger sitting next to me. He was actually acquainted with painting plants from RIPPERT and was full of praise. I find the cooperation in the works to be very helpful. The decision-making processes are short and the work is appreciated. The office equipment is top class, from the IT to the ergonomic desks. The location in East Westphalia is ideal, especially in my field of work. Many strong industrial companies are situated in the region, especially in mechanical engineering. That is a big advantage for me in conveying systems, because I know many partners and can get an idea of their solutions on site in an uncomplicated way. Personally, I have a weakness for aesthetics and creativity, which is why I like the modern design of the company headquarters a lot. I also still have time for hobbies. I’m a musician in a band and play drums and guitar. Sometimes I can also live out my creative streak at RIPPERT. For instance, I was largely involved in the development of the RIPPERT friction wheel conveying system.