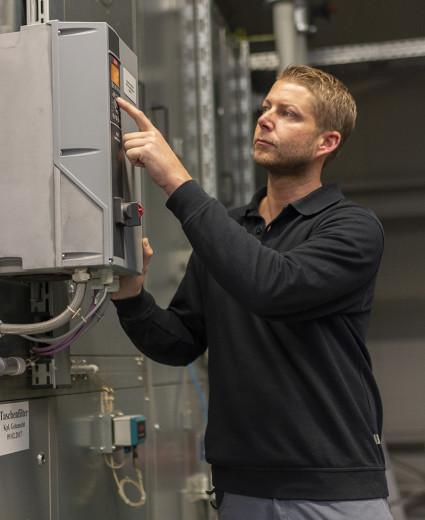
René Knoch – service technician Working as a service technician is perfect for me because it's a varied job where I get to travel a lot.
As a service technician, I work in the RIPPERT After-Sales area. My tasks include the annual maintenance, checking and repair of RIPPERT plants and, of course, the commissioning of new plants that are in use at our customers. I spend a lot of time on the road and get around a lot, which I very much like.
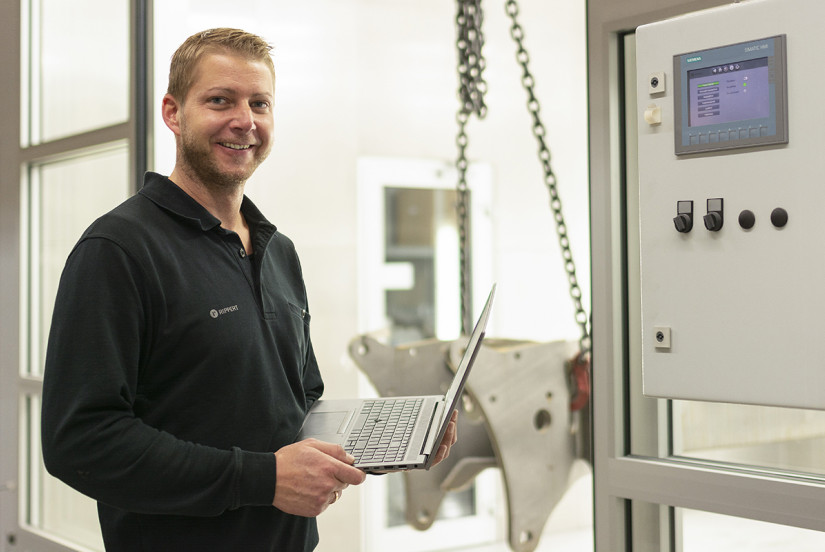
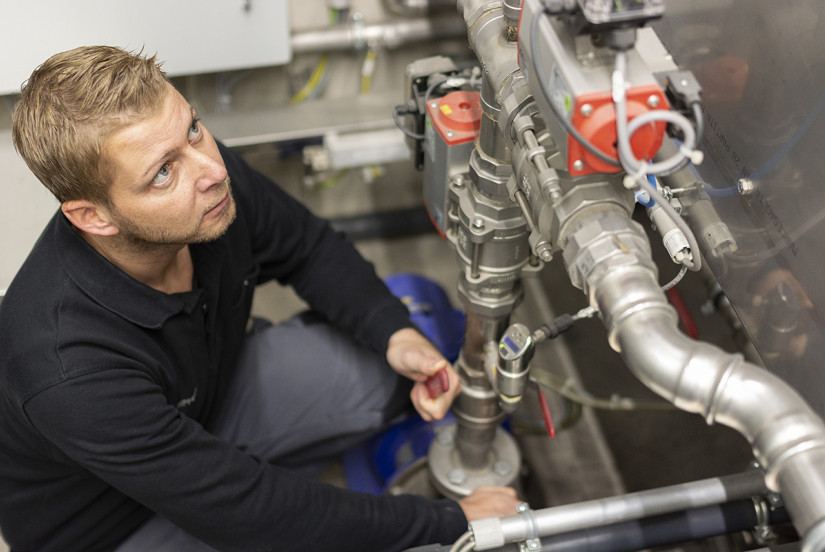
I travel by car to service assignments in Germany or nearby foreign countries such as Austria, Switzerland, Czechia or France, and by plane to service assignments further afield, such as Mexico or Dubai. Following my apprenticeship as a car mechanic, I worked for a few years for the German Navy as a drive technician on a frigate, after which I worked in a car workshop. However, since I like to be “on the move” in my job, I wasn’t satisfied with that in the long run. At that time a friend drew my attention to a job advertisement from RIPPERT and warmly recommended the company to me. I applied and got the job. That was in February 2016, since when I have been in action for RIPPERT and have never regretted taking this step. The work as a service technician is perfect for me, because on the one hand I have a very varied job and on the other I have sufficient time at home for family life. The work can be planned well. Our installation team arranges the dates and then coordinates them with me. Around 70 % of the dates are fixed in the long-term. In addition to that there are assignments at short notice – the so-called daily business. Sometimes I’m already back in the afternoon after visiting a customer, other times I’m on site for several days or weeks in order to thoroughly inspect a plant. The range of plants is large and extends from dedusting plants in the furniture industry to painting plants, cataphoretic painting plants and powder-coating plants in the automotive industry. It’s very variable. On site, it’s about carrying out the technical inspection in order to check existing plants for possible error and fault sources or to optimise and adjust them. Or, as already mentioned, it could be about the commissioning of new plants that are about to be handed over to the customer. In some cases I’m accompanied to commissioning by electricians and programmers, but mostly I’m alone at the customer. In the meantime, of course, I’m familiar with the various plants – but in the beginning that was a challenge. My first job, by the way, was a painting plant for a large tractor manufacturer. With my automotive knowledge I had to adjust in the early days, of course. However, it was lots of fun extending my knowledge. In general, I would say that the job as a service technician at RIPPERT requires technical understanding and interest in the various assignment topics. RIPPERT supports that with further training. I’ve taken several training courses, for example on explosion protection and fire dampers, and have qualified as an electrician. Other service technicians work alongside me and we exchange information on a regular basis. Each one has his own plants for which he is responsible – after all, our customers appreciate always having the same contact person at their disposal. However, we can also deputise for others where necessary. What I particularly like at RIPPERT is the social side. I can reconcile job and leisure very well. For example, if I need to take a day off at short notice, it’s no problem. Of course, it’s always give and take. If work occasionally has to be done at the weekend, then I do that, too.